Coating Environmental Protection Technology (VOC Organic Waste Gas Treatment Equipment) - Liangshi Coating Workshop Waste Gas Treatment Solution
Adsorption solvent recovery method
The adsorption solvent recovery process is the most widely used recovery technology at present. Its principle is to use the porous structure of adsorbent such as granular activated carbon, activated carbon fiber, or zeolite to capture organic substances in the exhaust gas; When the waste gas passes through the adsorption bed, the organic matter therein is adsorbed by the adsorbent in the bed layer, and the waste gas is purified; Due to the high price of adsorbent, it is necessary to carry out desorption regeneration and recycling.
After the adsorption of the adsorbent reaches saturation, water vapor is introduced to heat the adsorption bed, and the adsorbent is desorbed and regenerated. The organic matter is blown off and left the adsorption bed together with the water vapor to form a vapor mixture. Use a condenser to cool the steam mixture and condense it into a liquid.
The adsorption solvent recovery process uses an adsorbent to adsorb organic matter, then uses steam desorption, and finally directly separates or further distills the solvent that is insoluble in water. It is a combination of conventional adsorption methods and solvent recovery methods, characterized by simple operation and high efficiency, and is suitable for the treatment of VOCS waste gas with high concentration and single component, but it has large investment, large water vapor consumption, and operating costs for solvent recovery.
Liquid absorption method
Using a liquid solvent as an absorbent, the harmful components in the exhaust gas are absorbed by the liquid to achieve the purpose of purification. The absorption process is based on the principle of similar phase solubility of organic substances. Diesel oil and kerosene with high boiling points and low vapor pressure are often used as solvents to transfer VOC from the gas phase to the liquid phase, and then the absorption liquid is desorbed to recover the VOC therein, while allowing the solvent to be regenerated. This method can not only eliminate gaseous pollutants, but also recover some useful substances. It can be used to treat VOC with a gas flow rate of 3000~15000 m3/h and a concentration of 0.05%~0.5% (volume fraction), with a removal rate of 95%~98%; The purpose of organic waste gas treatment can be achieved.
Photooxygen catalytic purification method
Mechanism of degradation of organic waste gas: Active free radicals such as · OH, · O have extremely strong oxidation ability, can oxidize and decompose various organic compounds and some inorganic substances, can destroy the cell membrane of bacteria and solidify the protein of viruses, can kill bacteria and decompose organic pollutants, decompose organic pollutants into pollution-free water (H2O) and carbon dioxide (CO2), and thus have extremely strong sterilization, deodorization, mildew prevention, self-cleaning Air purification function.
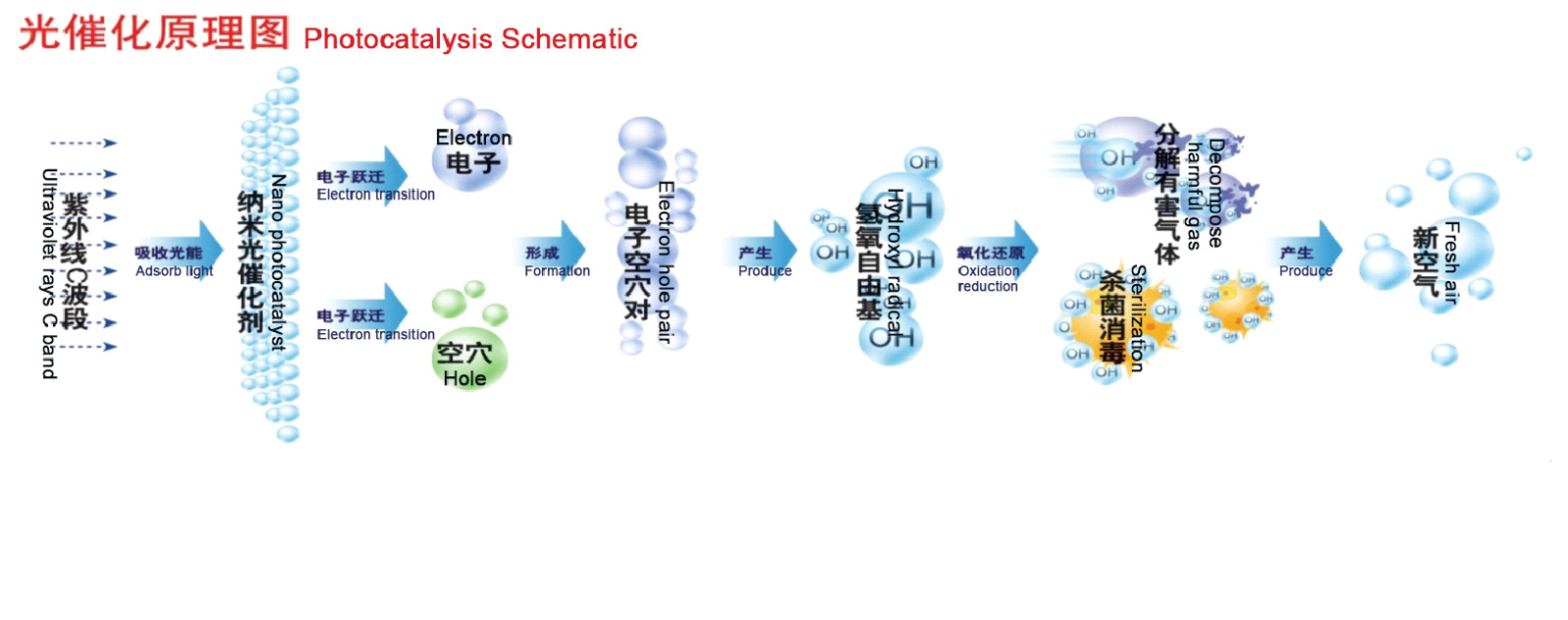
Product features:
Safety: Fully considering safety factors such as fire protection and explosion prevention, stable operation, safety and reliability. At the same time, temperature control technology is used to automatically alarm when the temperature exceeds a certain value.
Progressiveness technology: The internationally advanced photocatalyst technology can efficiently degrade volatile organic compounds (TVOC) and other pollutants such as benzene, toluene, xylene, styrene, formaldehyde, acetic acid, ammonia, etc., and release negative ions while decomposing pollutants. The photocatalyst material itself will not change and lose, and will continuously purify pollutants under light irradiation. It has a long lasting effect, and is safe and reliable. It is a new green environmental protection material.
Process maturity: The waste gas treatment process is mature and reliable, ensuring treatment efficiency, performance, and capacity, avoiding resource waste, secondary pollution, and safety hazards. And has repeatedly conducted waste gas treatment projects in the world's top 500 enterprises, such as the Olympic rowing epoxy resin odor purification project, the world's top 500 Aili Suzhou printing workshop, and the world's top 500 Foxconn coating workshop. 1. Low operating costs, ultra low fuel costs. When the concentration of organic waste gas is above 2000 PPM, the RTO device basically does not need to add auxiliary fuel; 2. High purification rate, generally above 98%; 3. Fully automatic control can be achieved, with simple operation, stable operation, and high safety and reliability; 4. There is no pulse phenomenon caused by pressure changes; 5. The temperature in the heat storage chamber is uniformly and gradually increased, which enhances heat transfer in the furnace, resulting in better heat exchange efficiency, small furnace volume, and reduced equipment cost; 6. Adopt staged combustion technology to release heat energy under delayed combustion; The furnace has uniform temperature rise, low burn loss, and good heating effect. There is no local high temperature and high oxygen zone that occurs during traditional combustion processes, which inhibits the generation of thermal nitrogen oxides (NOx) and has no secondary pollution; 7. An inert alumina ceramic ball is installed at the exhaust gas inlet to protect, buffer, and filter the heat storage ceramic, extending its service life.
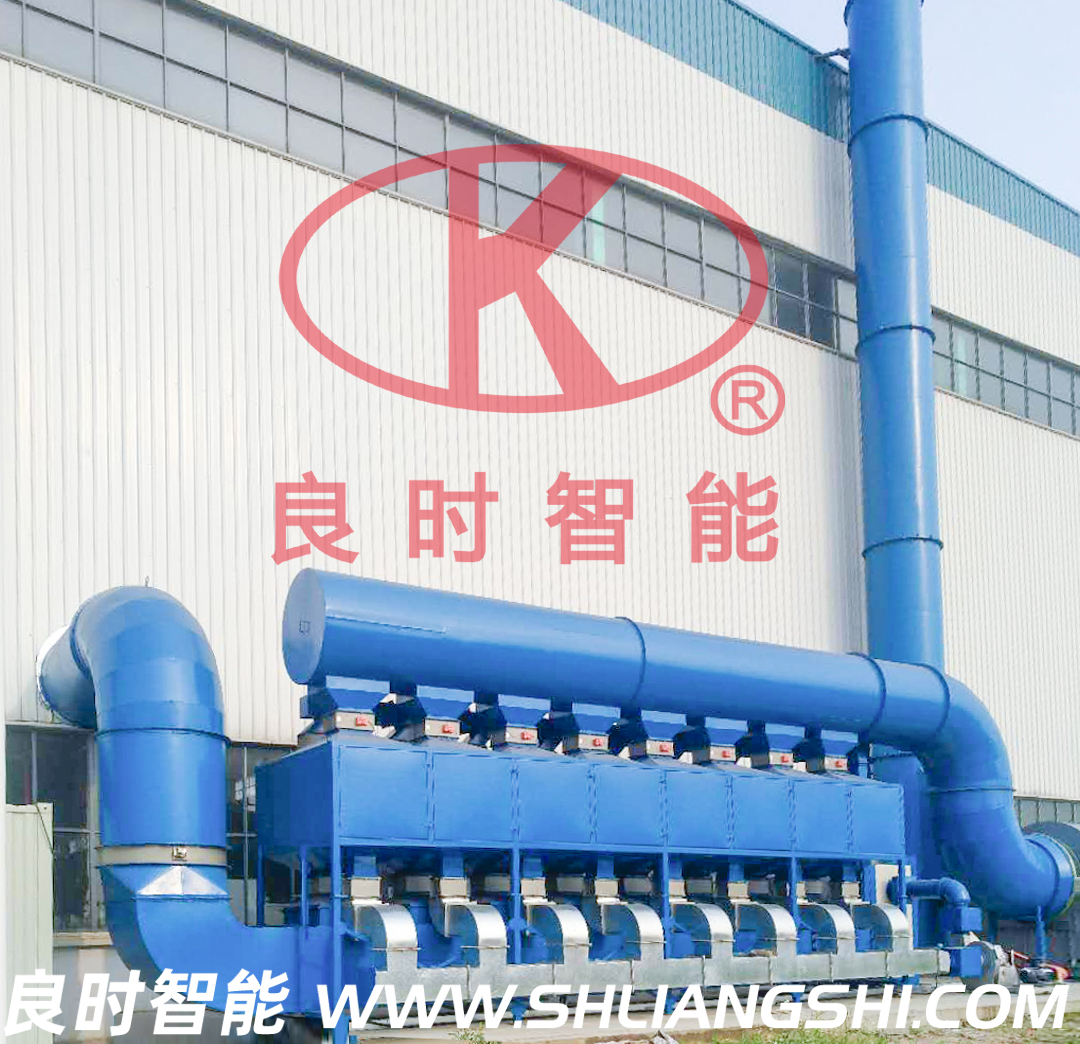
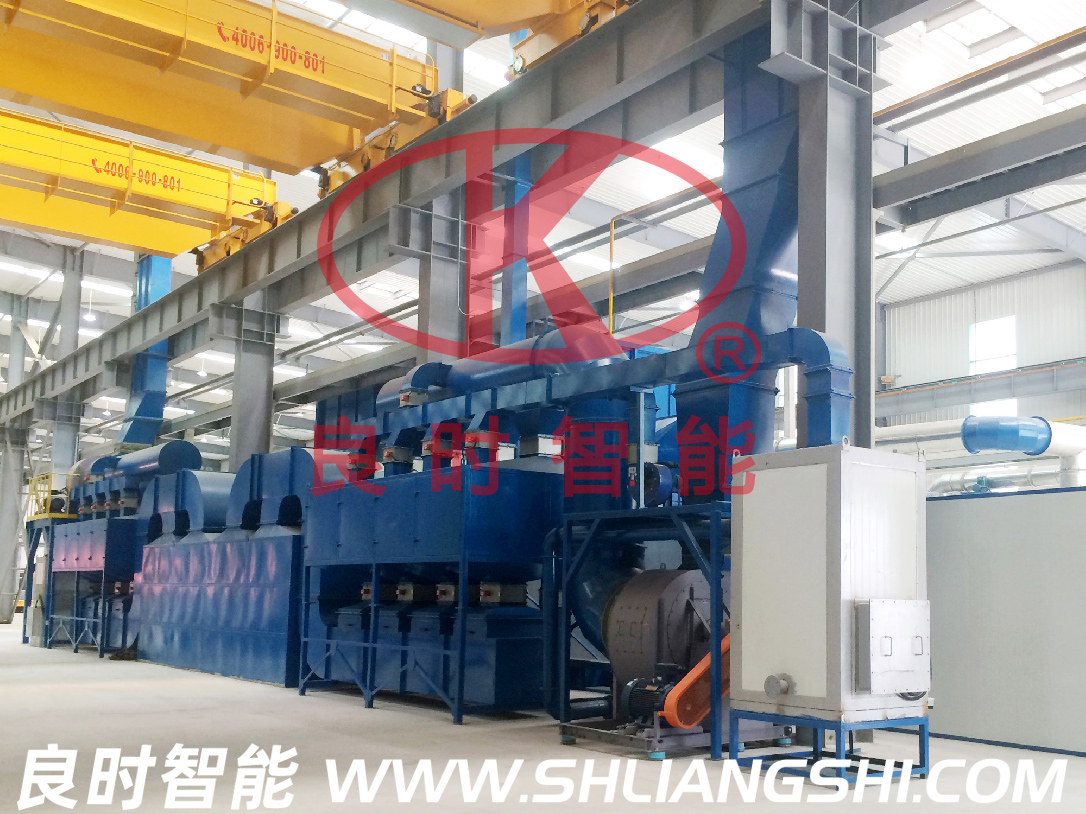
VOC organic waste gas treatment device
Regenerative incinerator
Regenerative thermal oxidizer. Regenerative Thermal Oxidizer (RTO) refers to the addition of a regenerative heat exchanger to a thermal oxidation device to preheat VOC exhaust gas before conducting oxidation reactions.
With the development of heat storage materials, the current heat recovery rate of regenerative heat exchangers has reached over 95%, and the occupied space is becoming smaller and smaller. In this way, the consumption of auxiliary fuel is small (even without auxiliary fuel, and when the VOC concentration reaches a certain value or above, heat can also be output from RTO). At the same time, due to the current selection of ceramic fillers as heat storage materials, it is possible to treat corrosive or particulate VOC exhaust gases.
Performance characteristics of RTO equipment
1. Low operating costs, ultra low fuel costs. When the concentration of organic waste gas is above 2000 PPM, the RTO device basically does not need to add auxiliary fuel;
2. High purification rate, generally above 98%;
3. Fully automatic control can be achieved, with simple operation, stable operation, and high safety and reliability;
4. There is no pulse phenomenon caused by pressure changes;
5. The temperature in the heat storage chamber is uniformly and gradually increased, which enhances heat transfer in the furnace, resulting in better heat exchange efficiency, small furnace volume, and reduced equipment cost;
6. Adopt staged combustion technology to release heat energy under delayed combustion; The furnace has uniform temperature rise, low burn loss, and good heating effect. There is no local high temperature and high oxygen zone that occurs during traditional combustion processes, which inhibits the generation of thermal nitrogen oxides (NOx) and has no secondary pollution;
7. An inert alumina ceramic ball is installed at the exhaust gas inlet to protect, buffer, and filter the heat storage ceramic, extending its service life.
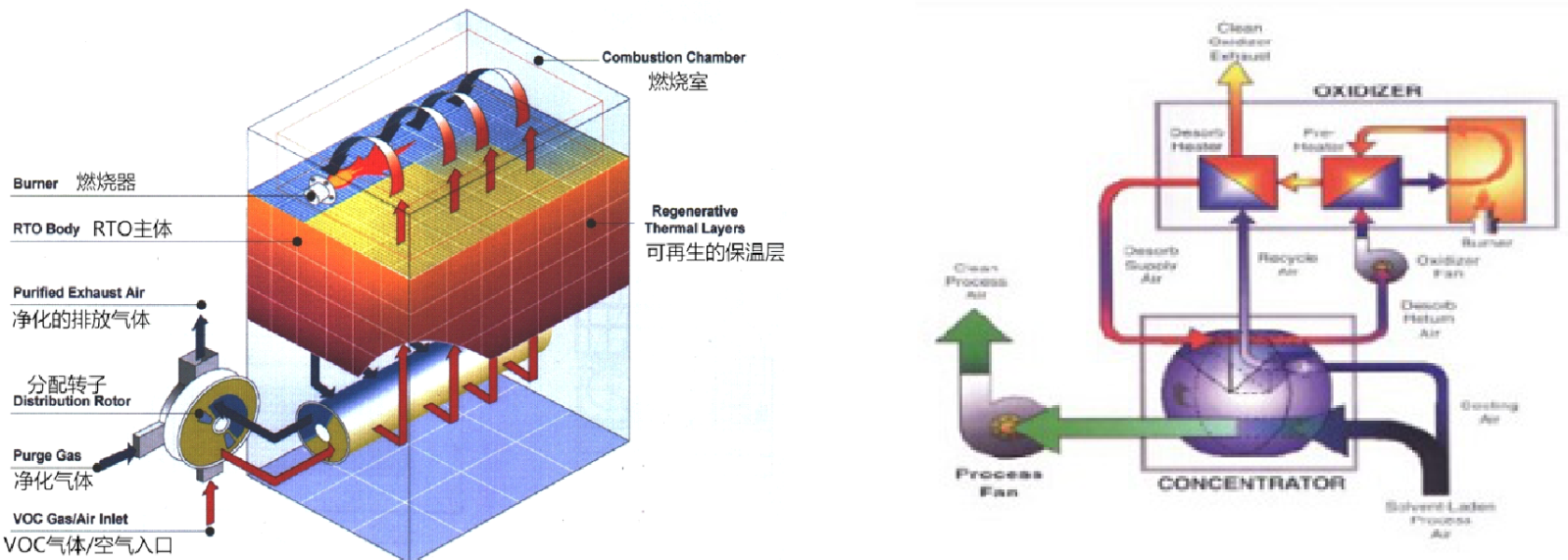
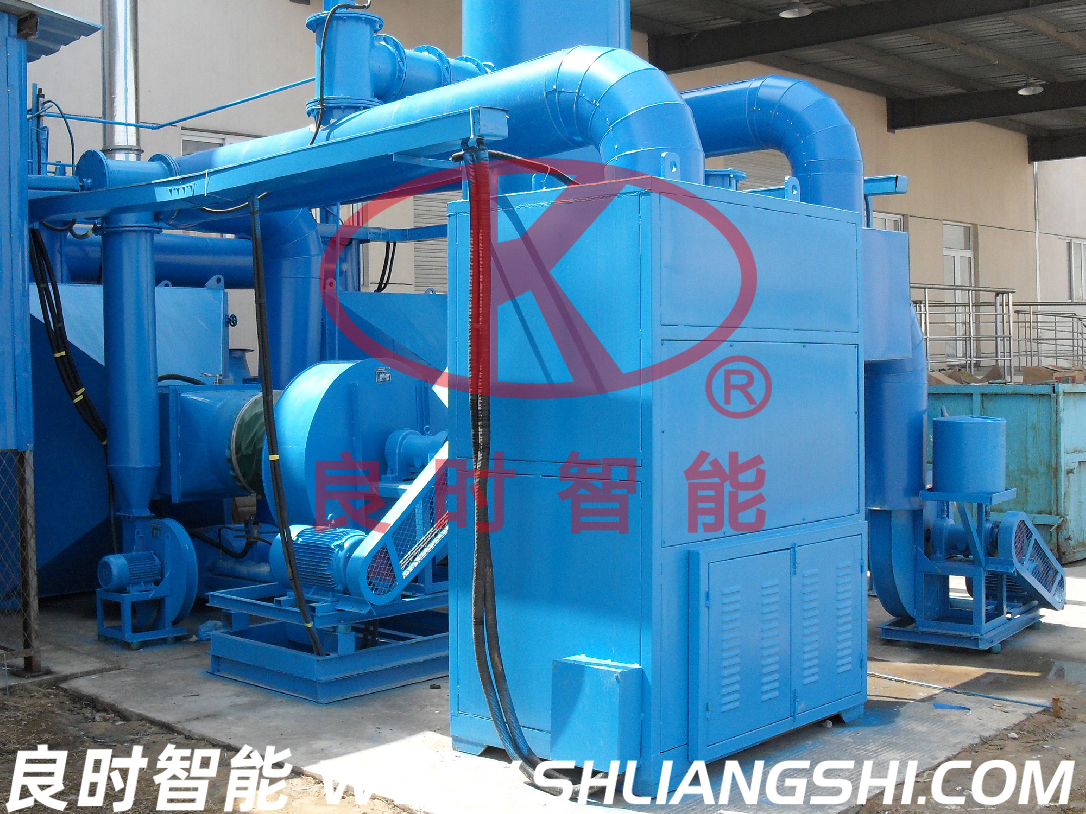
RCO organic waste gas catalytic combustion device
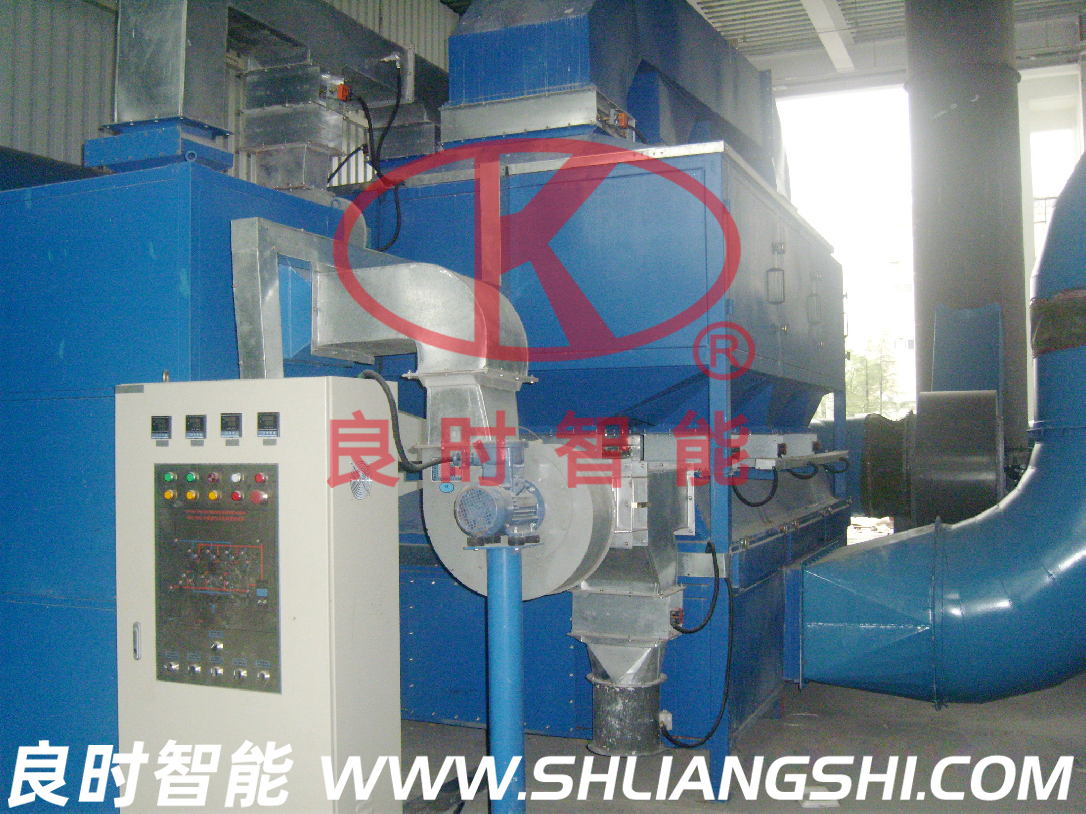
VOC organic waste gas treatment device
Catalytic combustion device
Regenerative catalytic combustion device (RCO) is a typical gas-solid catalytic reaction, whose essence is the deep concentration oxidation involving active oxygen. In the catalytic oxidation process, the role of the catalyst is to reduce the activation energy, while the surface of the catalyst has an adsorption effect, which enriches the reactant molecules on the surface, improving the reaction rate and accelerating the process of the reaction. With the aid of a catalyst, organic waste gas can undergo flameless combustion at a lower ignition temperature, and be oxidized and decomposed into CO2 and H2O. At the same time, a large amount of heat energy is emitted, thereby achieving the method of removing harmful substances in the waste gas.
Process flow (commonly used in spray painting production lines)
Through PLC automatic control, the concentration of organic matter in the desorbed gas stream can be increased by more than 10 times compared to that before the adsorption operation, and the gas flow rate is only about 1/20-1/10 of the total exhaust air volume, making the emission of large air volume and low concentration VOCS waste gas transformed into small air volume and medium to high concentration organic waste gas purification treatment. After this transformation, the heat energy generated by catalytic combustion of organic compounds can be effectively utilized and recovered, thereby reducing operating costs.
The organic waste gas is preheated by electric heating to the temperature required for catalytic reaction, and then flows through the catalyst bed. In the bed, the organic matter undergoes oxidation reaction to generate harmless carbon dioxide and water, and generates a large amount of heat.
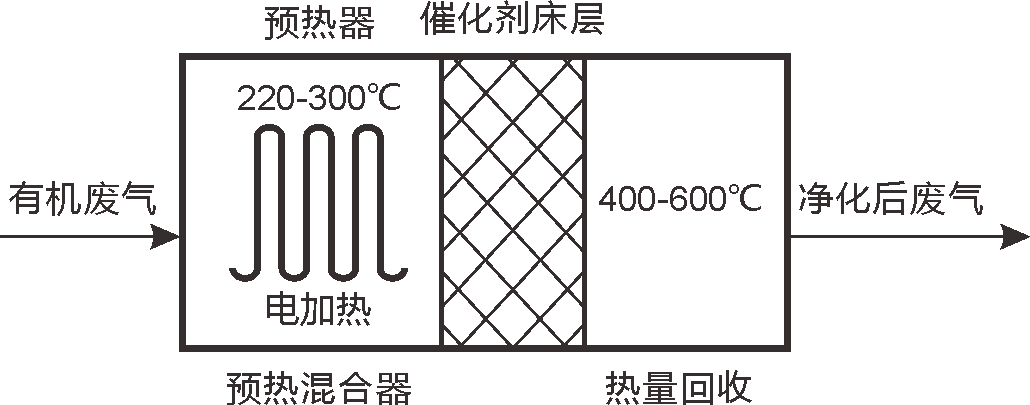
Process diagram of VOC organic waste gas treatment device
.jpg)
Product structure features:
1. Convenient operation: realize automatic control when the equipment is working;
2. Low energy consumption: It only takes 15-30 minutes for the equipment to start up to the ignition temperature (when the concentration of organic waste gas is high), and the energy consumption is only the power of the fan;
3. Safe and reliable: The equipment is equipped with a fire suppression system, an explosion-proof pressure relief system, an overtemperature alarm system, and an advanced automatic control system;
4. Low resistance, high purification efficiency: using today's advanced noble metal palladium, platinum impregnated honeycomb ceramic carrier catalyst, with a large specific surface area;
5. Reusable waste heat: The waste heat can be returned to the drying path, reducing the power consumption in the original drying path; It can also be used as a heat source for other aspects;
6. Small floor area: only 70% - 80% of similar products in the same industry, and no special requirements for equipment foundation;
7. Long service life: The catalyst is generally replaced within 4 years, and the carrier is renewable.
Equipment application range:
1. It can be used for purification treatment of organic solvents (mixed organic waste gases such as benzene, alcohol, ketone, aldehyde, ester, phenol, ether, and alkane);
2. Suitable for the purification of organic waste gases in industries such as electric wires, cables, enameled wires, machinery, electrical machinery, chemicals, instrumentation, automobiles, bicycles, motorcycles, engines, magnetic tapes, plastics, household appliances, etc;
3. It can be used in various drying lines such as drying channels, printing iron cans, surface spraying, printing ink, motor insulation treatment, leather shoes adhesive, etc., to purify the organic waste gas generated in various processes.
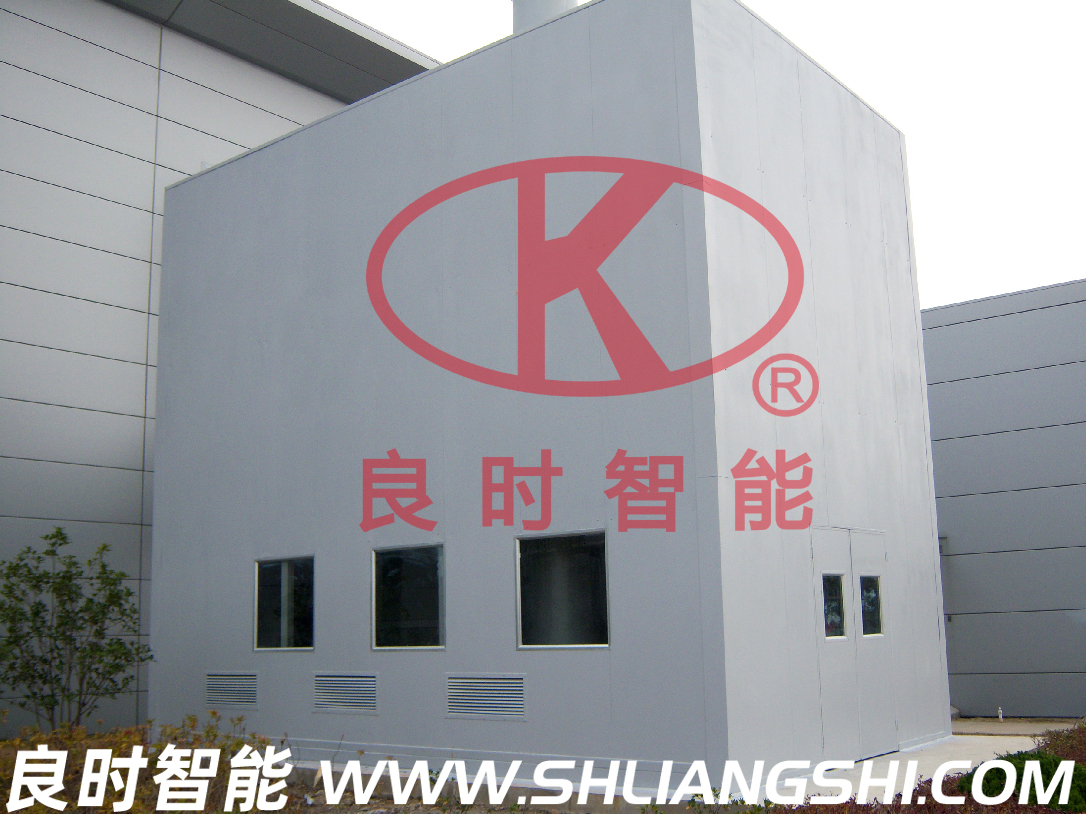
RTO, RCO, VOC organic waste gas treatment device
.jpg)
Adsorption solvent recovery method
The adsorption solvent recovery process is the most widely used recovery technology at present. Its principle is to use the porous structure of adsorbent such as granular activated carbon, activated carbon fiber, or zeolite to capture organic substances in the exhaust gas; When the waste gas passes through the adsorption bed, the organic matter therein is adsorbed by the adsorbent in the bed layer, and the waste gas is purified; Due to the high price of adsorbent, it is necessary to carry out desorption regeneration and recycling.
After the adsorption of the adsorbent reaches saturation, water vapor is introduced to heat the adsorption bed, and the adsorbent is desorbed and regenerated. The organic matter is blown off and left the adsorption bed together with the water vapor to form a vapor mixture. Use a condenser to cool the steam mixture and condense it into a liquid.
The adsorption solvent recovery process uses an adsorbent to adsorb organic matter, then uses steam desorption, and finally directly separates or further distills the solvent that is insoluble in water. It is a combination of conventional adsorption methods and solvent recovery methods, characterized by simple operation and high efficiency, and is suitable for the treatment of VOCS waste gas with high concentration and single component, but it has large investment, large water vapor consumption, and operating costs for solvent recovery.
Liquid absorption method
Using a liquid solvent as an absorbent, the harmful components in the exhaust gas are absorbed by the liquid to achieve the purpose of purification. The absorption process is based on the principle of similar phase solubility of organic substances. Diesel oil and kerosene with high boiling points and low vapor pressure are often used as solvents to transfer VOC from the gas phase to the liquid phase, and then the absorption liquid is desorbed to recover the VOC therein, while allowing the solvent to be regenerated. This method can not only eliminate gaseous pollutants, but also recover some useful substances. It can be used to treat VOC with a gas flow rate of 3000~15000 m3/h and a concentration of 0.05%~0.5% (volume fraction), with a removal rate of 95%~98%; The purpose of organic waste gas treatment can be achieved.
Photooxygen catalytic purification method
Mechanism of degradation of organic waste gas: Active free radicals such as · OH, · O have extremely strong oxidation ability, can oxidize and decompose various organic compounds and some inorganic substances, can destroy the cell membrane of bacteria and solidify the protein of viruses, can kill bacteria and decompose organic pollutants, decompose organic pollutants into pollution-free water (H2O) and carbon dioxide (CO2), and thus have extremely strong sterilization, deodorization, mildew prevention, self-cleaning Air purification function.