Fig. 1 Characteristic curve of residual stress distribution along the depth of shot peening
The selection of shot peening strengthening process parameters, such as shot peening intensity, shot peening time, shot medium, and shot flow rate, has a significant impact on the magnitude and distribution of residual stress values. At higher shot peening intensity, the projectile has greater kinetic energy during the incident stage, and the stress concentration of the sprayed material in the contact area is greater, resulting in a deeper deformation layer. Therefore, the maximum residual compressive stress value increases and the residual compressive stress layer deepens. However, excessive shot peening intensity may have the opposite effect, mainly due to factors such as stress relaxation and surface delamination. The effect of shot peening time is mainly limited to the saturation time, and the maximum residual stress value and stress layer depth increase with the extension of shot peening time. After reaching saturation, the values remain basically stable. The flow rate of the projectile directly affects the kinetic energy and 100% coverage time of the projectile. Under a certain shot pressure, if the flow rate of the projectile is high, the saturation time of the shot will be short, and the shot intensity will decrease, thereby affecting the magnitude and distribution of residual compressive stress. The larger the diameter of the projectile, the easier it is for shot peening to generate deeper residual compressive stress layers.
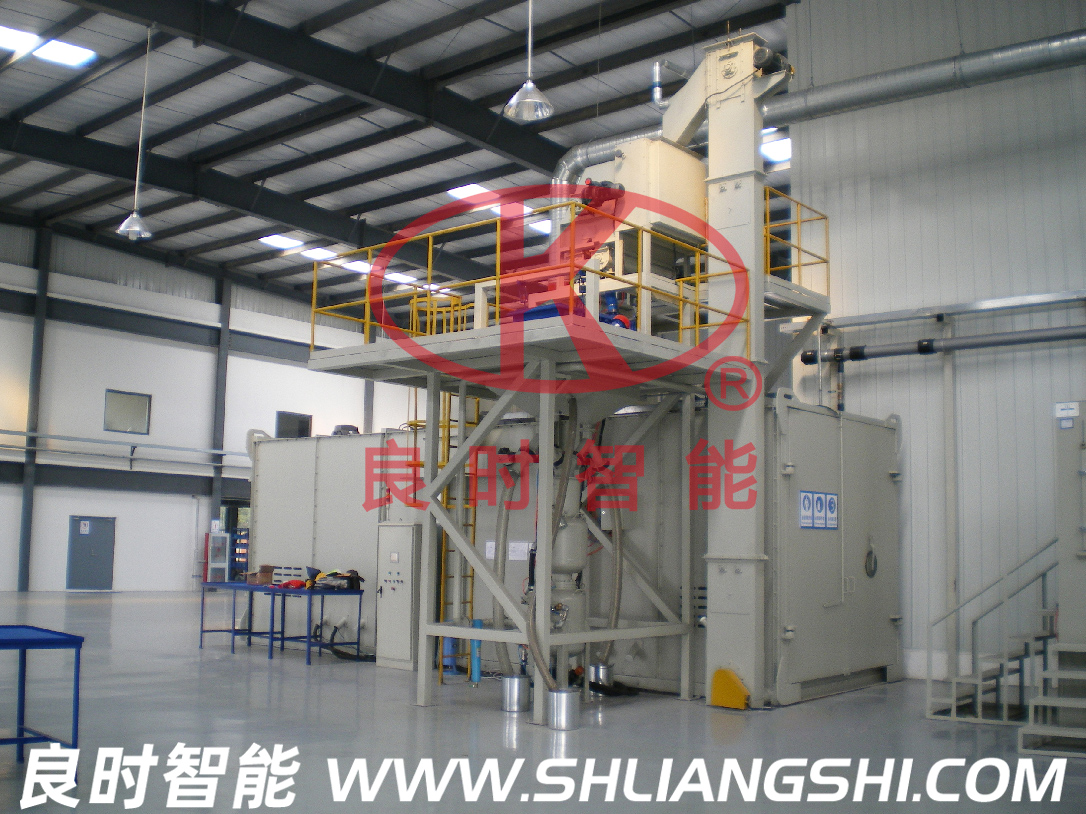
Aircraft component shot peening room system
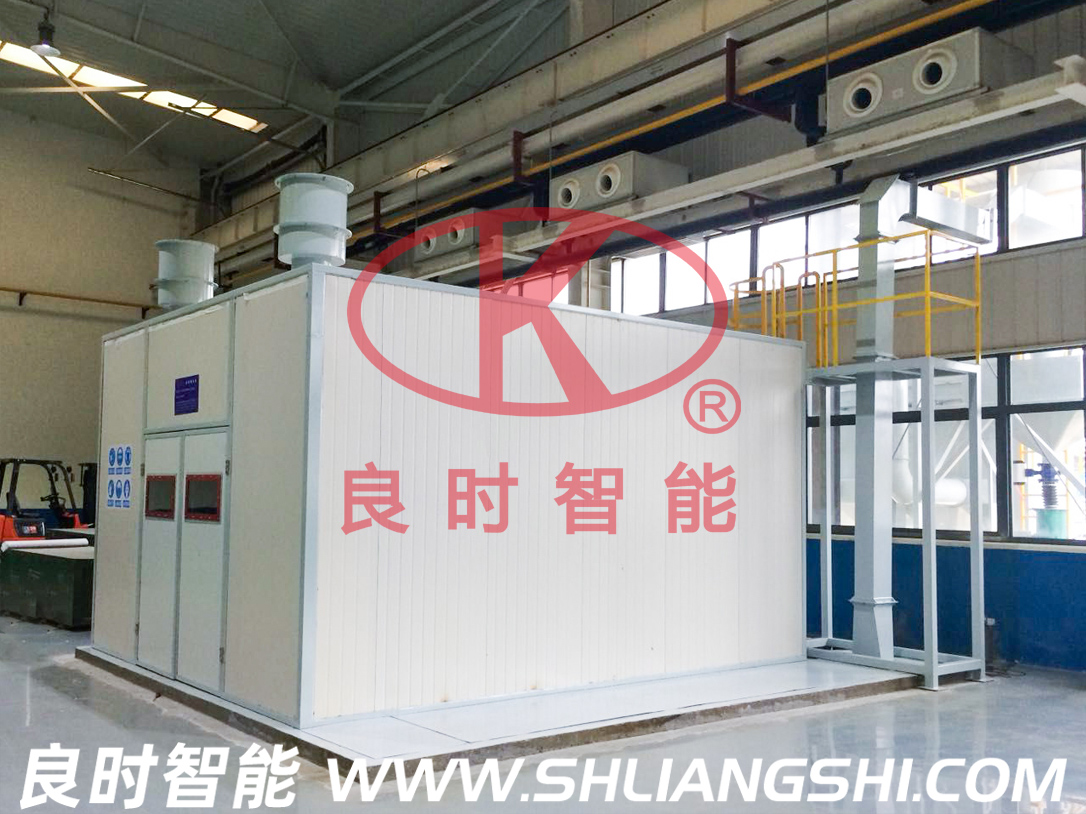
Aircraft landing gear sandblasting system
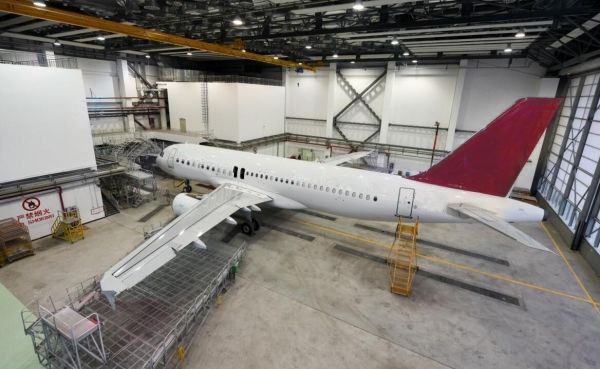
Aircraft dedicated coating room
The aviation industry has high requirements for its components, not only requiring lightweight materials, but also requiring them to withstand extreme loads in extremely harsh environments. By protecting the surface of parts from external damage and extending fatigue life, our shot peening surface treatment technology can greatly improve the overall performance of the parts. The vast majority of components used in the aviation industry, including aircraft frames, wings, engines, engine blades, blade tenons, blade turntables, landing gears, driving devices, or transmission parts (gears), all use precision shot peening technology to meet their material performance indicators.
Shot peening strengthening is the process of high-speed projectile flow spraying the surface of a material and causing plastic deformation of its surface. During the shot peening process, the bullet repeatedly strikes the surface of the material, ultimately creating a plastic deformation layer near the material surface, which is a strengthening layer with a certain depth. Reasonable introduction of the surface plastic deformation layer for shot peening strengthening can significantly improve the fatigue performance and stress corrosion resistance of the material. According to the plastic deformation layer, grain refinement within the deformation layer, and changes in metallographic structure generated during strengthening, the material can be divided into the following three types of strengthening:
1. Residual compressive stress field (stress strengthening)
2. Deformation microstructure (tissue strengthening)
3. Transformation from retained austenite to martensite (transformation strengthening)
Shot peening classification: Shot peening is often divided into three types according to its application scope:
① Shot peening strengthening (strong shot peening) ② Shot peening forming ③ Shot peening cleaning.
Shot peening is a widely used surface strengthening technology, characterized by simple process operation and significant strengthening effects. It is an effective method for improving and enhancing the fatigue and stress corrosion fracture resistance of components.
For components with the following characteristics, surface shot peening strengthening treatment should be given priority consideration.
A) Important load-bearing components that withstand alternating loads and are prone to fatigue failure
B) Important load-bearing components that are prone to stress corrosion (or hydrogen embrittlement) failure under the combined action of constant load and corrosive environment
C) Various steel forgings with tensile strength exceeding 1400MPa
D) Steel components that require electroplating with Cr, Ni, Ni+Cd, Cd+Ti, etc
E) High strength aluminum alloy components that require anodizing treatment
F) Areas with stress concentration (such as inner and outer fillets, keyways, welds, tool markings, imprint markings, and structural mutation areas)
G) The area about 30mm to the left and right of the weld seam
H) Various types of spiral compression springs
The methods for evaluating the effectiveness of shot peening include: 1. surface roughness measurement 2. residual stress measurement 3. microstructure analysis 4. microhardness testing fatigue strength test. To achieve the expected strengthening effect of shot blasting, it is necessary to strictly control its three major elements (1. Equipment 2. Media 3. Process parameters)
Shot peening strengthening process parameters:
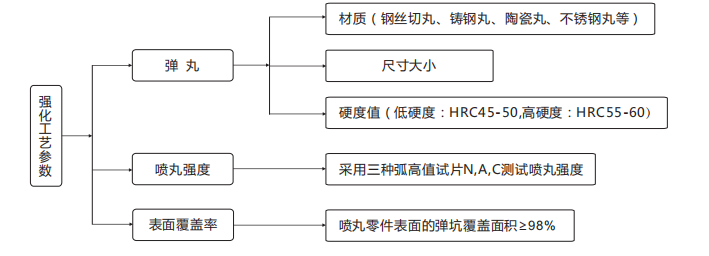
.jpg)
飞机专用涂装房
航空锻件专用热处理喷丸室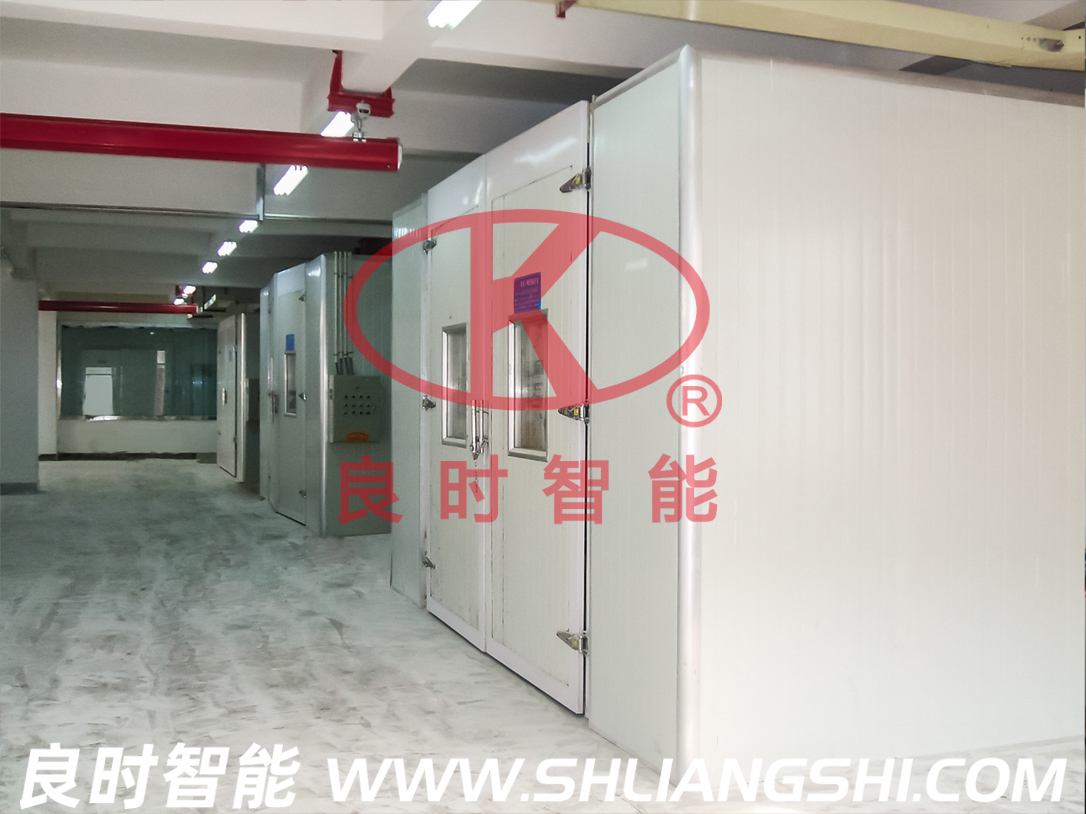
Aviation equipment plasma spraying room
.jpg)
Regarding Liangshi Intelligence:
Liangshi Intelligent (stock code: 837430) is located in the Lingang New Area of China (Shanghai) Pilot Free Trade Zone. The production base of Liangshi Intelligent Lingang New Area covers an area of 84 acres (approximately 56000 square meters) and has first-class customer information sources and product marketing channels. Its products are sold to more than 20 countries worldwide.
Liangshi Intelligent has passed the Sira International Quality Management System certification and ISO14001 Environmental Management System certification in the UK, and has obtained more than 30 utility model patents and invention patents. Its affiliated company Shanghai Liangshi Pressure Vessel Manufacturing Co., Ltd. has obtained a special equipment design license (number: TS1231092-2017, engaged in the design of D1 and D2 pressure vessels), Special Equipment Manufacturing License (No. TS2231129-2016, engaged in the manufacturing of D1 and D2 pressure vessels), and has formed close cooperation with major universities. Relying on high-tech, relying on high-quality products and excellent after-sales service, we have created good economic and social benefits.
Shanghai Liangshi Intelligent Technology Co., Ltd. provides surface treatment system solutions to global customers with over 20 years of experience. It is a professional manufacturing and automation intelligent control system integration company that integrates research and development, design, manufacturing, engineering installation, and engineering consulting. It can provide customers with:
1. Surface treatment shot blasting, shot strengthening equipment, thermal spraying and coating equipment process system solutions and process equipment;
2. Automation and robot application process system solutions and process equipment;
3. Integrated solutions for pressure bearing systems in the fields of food and dairy products, pharmaceuticals, biology, refrigeration, petrochemical, shipbuilding, energy, paper making, textile systems;
4. Coating environmental protection equipment: VOC exhaust gas, wastewater, dust treatment and noise control system process solutions and equipment.
The leading products of the enterprise are as follows:
Main business: Design, research and development, production, and sales of surface treatment engineering system integration.
Six main products: automated coating production lines, intelligent robot spraying systems, automated shot blasting production lines, intelligent robot shot blasting strengthening systems, automated thermal spraying systems, and energy-saving and environmental protection equipment for coating.
The products are mainly used in fields such as new materials, new energy, engineering machinery, automobile manufacturing, containers, ship and ocean engineering, aerospace, port and bridge, electronic and electrical, environmental engineering, printing and papermaking machinery, medical machinery, textile machinery, etc.
Main customer groups: aerospace carriers, land and navy military industry, automotive locomotives and high-speed trains, petrochemical power, shipbuilding and port machinery, new materials and new energy, heavy industry equipment, agricultural machinery engineering machinery and mechanical manufacturing equipment, etc.
The surface engineering system integration produced by the company has the characteristics of intelligence and automation, which can achieve automatic control of industrial production processes, and therefore belongs to automation equipment. According to the definition of high-end equipment in the "Twelfth Five Year Plan" for the high-end equipment manufacturing industry, "it mainly includes high-tech and high value-added equipment required for the transformation and upgrading of traditional industries and the development of strategic emerging industries." The company's products belong to high-end equipment and are strategic industries that provide technical equipment for other industries in the national economy.
For more information, please visit www.shliangshi.com
Tel: 021-5103520068913886
Emergency service: 18918186798
National service: 400-021-5767
Fax: 021-68907128
Email: webmaster@shliangshi.com