The development process of anti-corrosion for steel bridges in Europe and America is as follows: in the 1940s, it was paint anti-corrosion; In the 1950s and 1970s, heavy-duty anti-corrosion coatings, hot-dip galvanizing, flame spraying, and arc spraying coexisted; After the 1980s, with the development of arc spraying technology, arc spraying anti-corrosion was widely used. Initially, zinc was mostly sprayed, but now arc spraying aluminum is gradually becoming the trend of anti-corrosion development. After the 1990s, with the increasing frequency of international exchanges, some technologically advanced heavy-duty anti-corrosion coating brands from Europe and America have successively entered China, such as AkzoNobel, Hempel from Denmark, Sigma from the Netherlands, and other internationally renowned coating companies have successively established factories in China, objectively promoting the development of domestic heavy-duty anti-corrosion technology and gradually improving the traditional mode of China's lead based coating system, Formed a heavy-duty anti-corrosion technology with metal spraying and zinc containing coatings as the core.
The surface treatment before painting of heavy-duty anti-corrosion coatings The surface treatment level before painting of heavy-duty anti-corrosion coating primer is usually Sa2.5-Sa3.0 cleanliness and 25-70 relative roughness μ m. Surface treatment usually uses sandblasting, shot blasting, and other spray rust removal methods, and local small areas can be mechanically derusted to St3 level. In special cases, such as water-based inorganic zinc rich coatings, the surface treatment level is required to be higher, and sometimes the cleanliness requirement must reach the surface treatment level of metal spraying.
Liangshi Intelligent (stock code: 837430) has designed and manufactured a sandblasting and painting room (sandblasting room/painting room) system engineering for the anti-corrosion coating project of the steel structure and bridge box of the Hong Kong Zhuhai Macao Bridge main project. The sandblasting and painting room system equipment has been meticulously worked by company employees for several months and passed the final acceptance in one go recently, It is also the only supplier of sandblasting coating room equipment system in the industry that has passed the final acceptance at one time. This acceptance is particularly strict. The acceptance units include experts from Hong Kong-Zhuhai-Macao Bridge Authority, CCCC Highway Planning and Design Institute, Shanghai Municipal Engineering Design Institute, Wuhan Bridge Construction Engineering Supervision Company, China Classification Society and Wuchuan Heavy Engineering Co., Ltd. Being able to pass the final acceptance at once fully reflects the scientific and innovative process of Shanghai Liangshi's meticulously researched, designed, manufactured, installed, and debugged system, setting an example for the same industry.
.jpg)
Sand blasting and coating room for steel structure of a certain heavy industry bridge.jpg)
Sandblasting, suction, and dust removal equipment for painting central rooms
The corrosion rate of steel structures follows: ① fast first and then slow; ② Fast in coastal or humid environments; ③ The heavy industrial zone is twice that of the urban area and 10 times that of mountainous and rural areas; ④ 5 times faster without rust prevention layer than with rust prevention layer; ⑤ Outdoor is four times larger than indoor. Corrosion prevention of steel structures is an important issue that must be addressed in the design, construction, and use of steel structures. It involves many issues such as durability, cost, performance, and maintenance costs of steel structures.
The rust removal process for steel structures is a prerequisite and guarantee for corrosion prevention. Common surface treatment methods include:
1. Manual processing. By hand, the oxide skin and rust on the surface of the workpiece can be removed, but manual cleaning is not thorough, resulting in poor quality and low production efficiency.
2. Chemical treatment. The main method is to use alkaline or acidic solutions to dissolve the oil stains and oxides on the surface of the workpiece in alkaline or acidic solutions, in order to remove the oxide skin, rust, and oil stains on the surface of the workpiece. But if the time is not properly controlled, even with the addition of corrosion inhibitors, it can still cause excessive corrosion of the steel. For more complex structural components and parts with holes, if not handled properly, the residual acid immersed in the holes or gaps will be difficult to completely remove, which will become a hidden danger. Therefore, chemical treatment is suitable for cleaning thin plate parts. Moreover, chemical substances are prone to volatilization and have high costs. Improper treatment of chemical emissions can cause serious pollution to the environment. With the increasing awareness of environmental protection among people, this treatment method is being replaced by mechanical treatment.
3. Mechanical treatment method. Mainly including shot peening method and shot blasting method. Shot peening is also divided into shot peening and sandblasting. Surface treatment using shot peening has a high impact force and obvious cleaning effect. However, shot peening can easily deform thin sheet workpieces and cannot completely remove oil stains. The best cleaning effect should also be sandblasting, which is suitable for cleaning the surface of workpieces with high requirements. Shot blasting cleaning is a method of using centrifugal force to accelerate the projectile and spray it onto the workpiece for rust removal and cleaning. After the completion of welding of H-shaped steel components, they enter the enclosed space for shot blasting and rust removal. Shot blasting can be carried out on the surface of the steel components below the moderate rust level. In addition to its rust removal function, the shot blasting and rust removal process can also eliminate residual stress generated after the completion of welding of H-shaped steel components and improve the stress state of the steel components after applying loads. The use of shot blasting equipment for rust removal has the characteristics of longer corrosion resistance and improved stress state of components compared to traditional manual rust removal and sandblasting rust removal. However, shot blasting is limited by the site, which can easily create dead corners on the inner surface of the workpiece that cannot be cleaned. The equipment structure is complex, and parts such as blades wear quickly, resulting in high one-time investment costs.
There are many reasons for steel corrosion, which can be divided into two categories based on different environmental media: chemical corrosion and electrochemical corrosion.
Chemical corrosion, also known as dry corrosion, refers to the oxidation or sulfurization of steel at room or high temperatures. The oxidation of steel is formed by chemical reactions that occur when it comes into contact with oxidizing media. Oxidative media include air, oxygen, water vapor, carbon dioxide, sulfur dioxide, and chlorine, which react to form loose oxides. The reaction speed accelerates with the increase of humidity and temperature, especially in the alternating dry and wet environment where corrosion is more severe.
Electrochemical corrosion, also known as wet corrosion, is the corrosion caused by localized battery action on the surface of steel due to electrochemical phenomena. Steel is covered with an extremely thin water film on its surface due to adsorption in humid air. Due to uneven surface composition or force deformation, there is a difference in electrode potential between adjacent parts, forming many micro batteries. In the anode region, iron is oxidized into iron ions and enters the water film. Oxygen from air is dissolved in water. In the cathode region, oxygen is reduced to OH ions, which combine to form insoluble iron (oh) 2 and further oxidize to form loose and easily peeled rust iron (oh) 3. The corrosion of steel in the atmosphere is caused by both chemical and electrochemical corrosion, but electrochemical corrosion is the main cause. According to the degree of corrosion of exposed steel plates in the environment, ISO 12944 divides the atmospheric corrosion level into five levels. For different corrosion environments and anti-corrosion years, ISO 12944 provides guidance on the selection of anti-corrosion coating systems and specifies the minimum dry film thickness of the coating system. For example, for the atmospheric corrosive environment of c4 and a high corrosion resistance period (greater than 15 years), a 75 micron epoxy zinc rich primer, a 150 micron epoxy mica iron intermediate paint, and a 50 micron polyurethane topcoat can be selected, witha total dry film thickness of 275 microns.
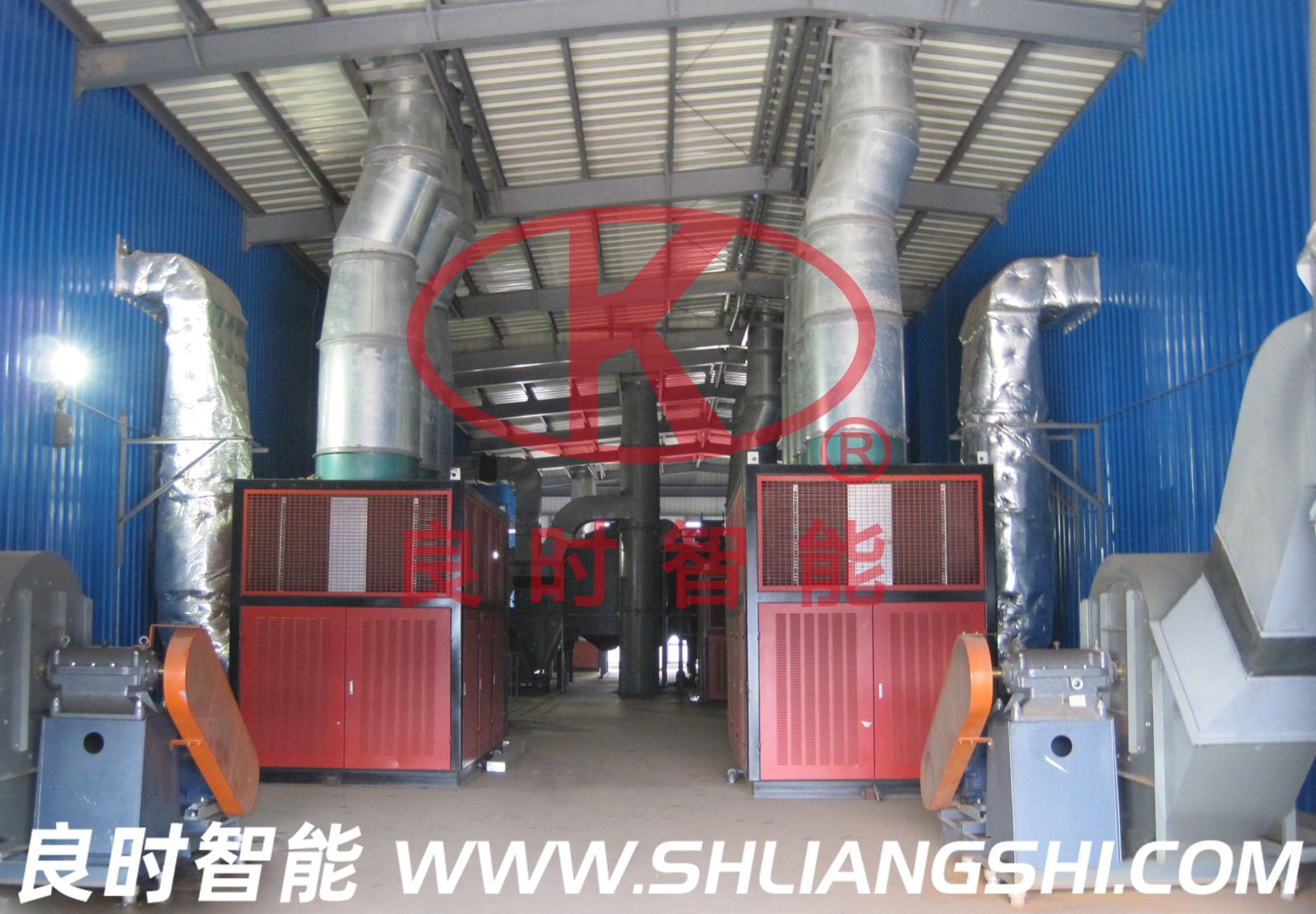
Dehumidification, air source, and waste gas treatment equipment for painting central rooms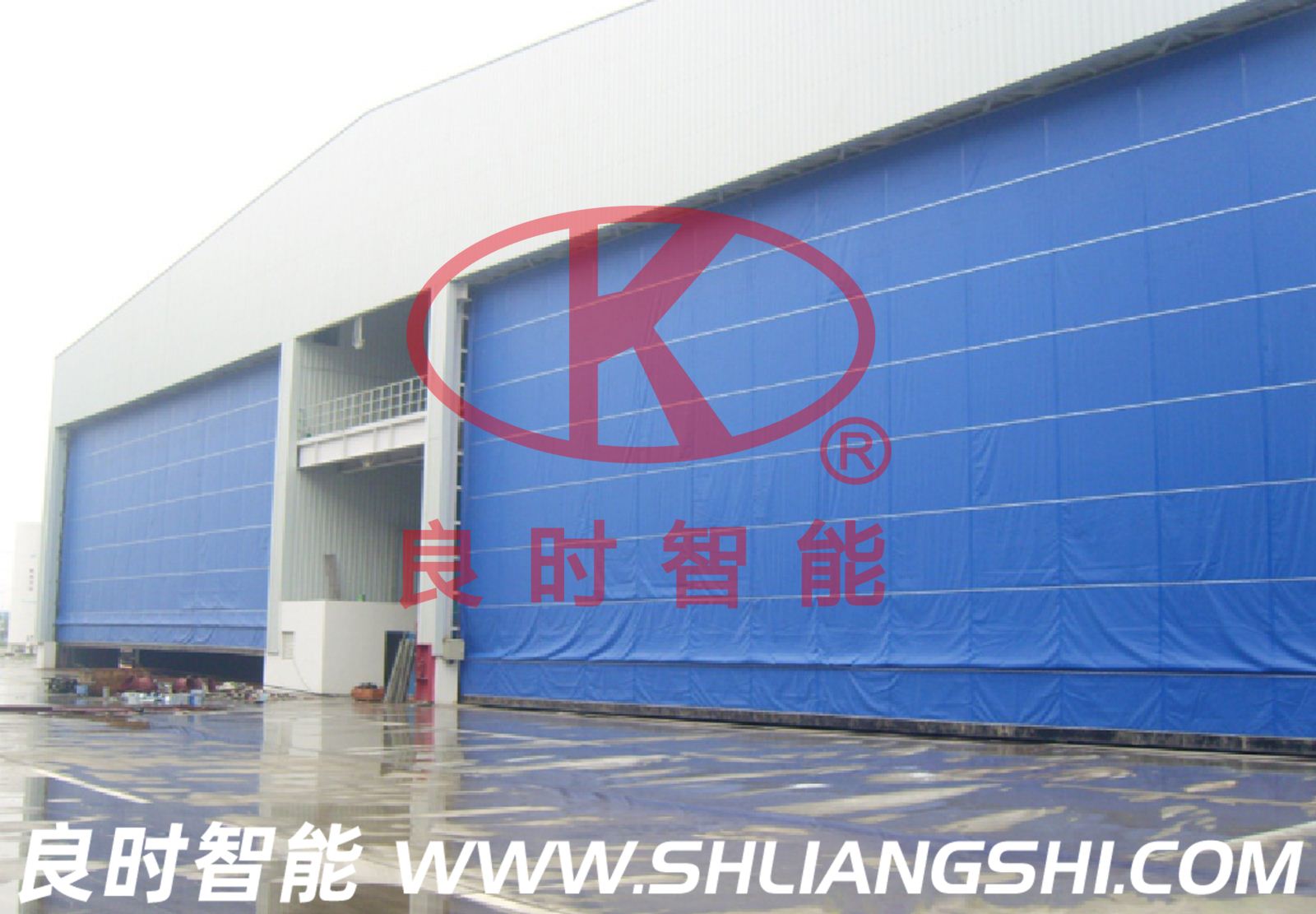
Chemical equipment, shield machinery equipment, sandblasting and spraying coating room
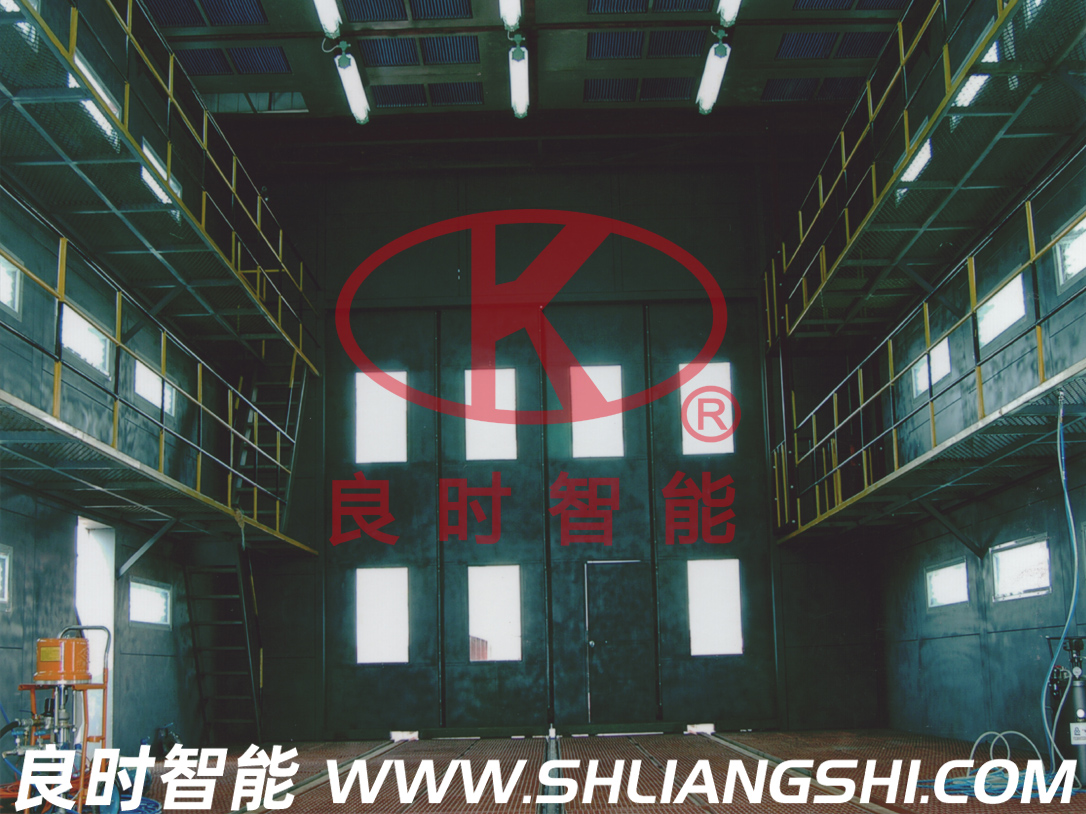
Miner's mechanical sandblasting room spray painting room
.jpg)
Regarding Liangshi Intelligence:
Liangshi Intelligent (stock code: 837430) is located in the Lingang New Area of China (Shanghai) Pilot Free Trade Zone. The production base of Liangshi Intelligent Lingang New Area covers an area of 84 acres (approximately 56000 square meters) and has first-class customer information sources and product marketing channels. Its products are sold to more than 20 countries worldwide.
Liangshi Intelligent has passed the Sira International Quality Management System certification and ISO14001 Environmental Management System certification in the UK, and has obtained more than 30 utility model patents and invention patents. Its affiliated company Shanghai Liangshi Pressure Vessel Manufacturing Co., Ltd. has obtained a special equipment design license (number: TS1231092-2017, engaged in the design of D1 and D2 pressure vessels), Special Equipment Manufacturing License (No. TS2231129-2016, engaged in the manufacturing of D1 and D2 pressure vessels), and has formed close cooperation with major universities. Relying on high-tech, relying on high-quality products and excellent after-sales service, we have created good economic and social benefits.
Shanghai Liangshi Intelligent Technology Co., Ltd. provides surface treatment system solutions to global customers with over 20 years of experience. It is a professional manufacturing and automation intelligent control system integration company that integrates research and development, design, manufacturing, engineering installation, and engineering consulting. It can provide customers with:
1. Surface treatment shot blasting, shot strengthening equipment, thermal spraying and coating equipment process system solutions and process equipment;
2. Automation and robot application process system solutions and process equipment;
3. Integrated solutions for pressure bearing systems in the fields of food and dairy products, pharmaceuticals, biology, refrigeration, petrochemical, shipbuilding, energy, paper making, textile systems;
4. Coating environmental protection equipment: VOC exhaust gas, wastewater, dust treatment and noise control system process solutions and equipment.
The leading products of the enterprise are as follows:
Main business: Design, research and development, production, and sales of surface treatment engineering system integration.
Six main products: automated coating production lines, intelligent robot spraying systems, automated shot blasting production lines, intelligent robot shot blasting strengthening systems, automated thermal spraying systems, and energy-saving and environmental protection equipment for coating.
The products are mainly used in fields such as new materials, new energy, engineering machinery, automobile manufacturing, containers, ship and ocean engineering, aerospace, port and bridge, electronic and electrical, environmental engineering, printing and papermaking machinery, medical machinery, textile machinery, etc.
Main customer groups: aerospace carriers, land and navy military industry, automotive locomotives and high-speed trains, petrochemical power, shipbuilding and port machinery, new materials and new energy, heavy industry equipment, agricultural machinery engineering machinery and mechanical manufacturing equipment, etc.
The surface engineering system integration produced by the company has the characteristics of intelligence and automation, which can achieve automatic control of industrial production processes, and therefore belongs to automation equipment. According to the definition of high-end equipment in the "Twelfth Five Year Plan" for the high-end equipment manufacturing industry, "it mainly includes high-tech and high value-added equipment required for the transformation and upgrading of traditional industries and the development of strategic emerging industries." The company's products belong to high-end equipment and are strategic industries that provide technical equipment for other industries in the national economy.
For more information, please visit www.shliangshi.com
Tel: 021-5103520068913886
Emergency service: 18918186798
National service: 400-021-5767
Fax: 021-68907128
Email: webmaster@shliangshi.com